3 Examples of How IoT Technology Has Transformed Manufacturing
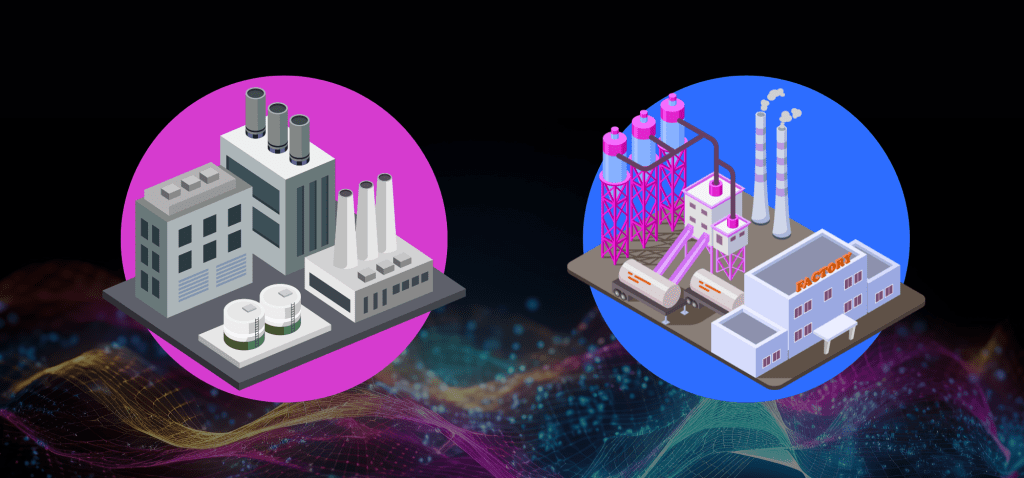
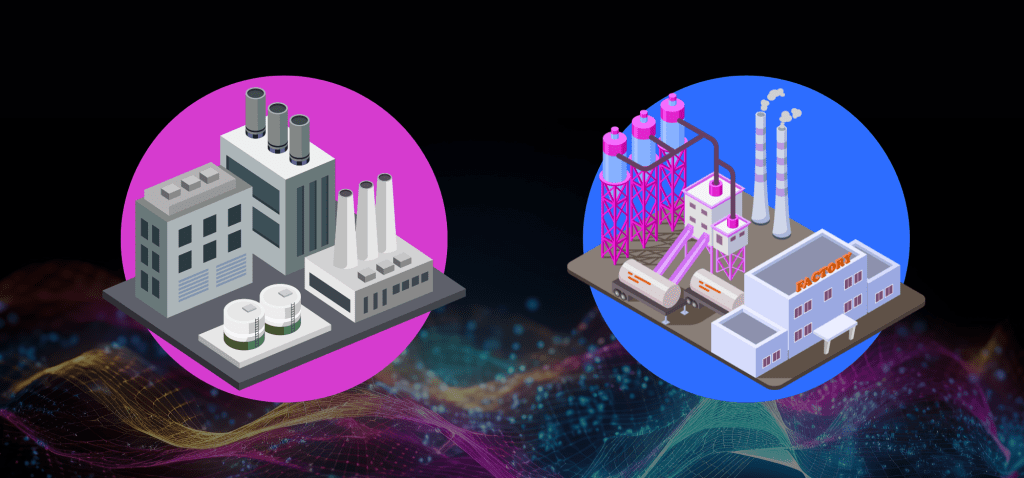
Almost every industry has turned to IoT (Internet of Things) to automate and optimise their processes. Manufacturing companies are among the most influenced by IoT-enabled systems; over the years, it’s become an increasing trend for businesses looking to take advantage of monitoring and tracking, faster networks, and more innovative devices.
IoT technology has paved the way for Industry 4.0, a technology and innovation-centric era. By integrating IoT systems and sensors into everyday operations, manufacturers can enhance and upscale all stages of their production process and manufacturing operations while reducing equipment failure and unplanned downtime.
IoT Applications in the Manufacturing Industry
Industrial Internet of Things (IIoT) innovations have long been commonplace on factory floors thanks to their unmatched precision, speed, and accuracy. With IoT systems, manufacturers can take their robotics initiatives further, enabling data collection and sharing, intercommunication with other devices on the production line, and autonomous coordination of activities.
In other manufacturing operations areas, IoT technology plays a key role. Its proficiency in predictive maintenance, asset management, product quality control, inventory management, and energy management makes it a versatile and efficient option for any manufacturer. Some more detailed use cases include:
Automation and Smart Manufacturing
IoT-enabled factories can automate various aspects of communication and coordination, enhancing their ability to complete time-sensitive tasks using cutting-edge IoT technology.
For example, IIoT allows for deploying advanced robotics that perform complex tasks with high precision. ‘Cobotics’—a term for collaborative robots—work alongside human operators to enhance productivity and promote factory safety.
Autonomous material handling is also becoming more commonplace within manufacturing facilities; automated guided vehicles (AGVs) and drones manage material transport. These technologies help streamline workflows by reducing manual labour and minimising errors in inventory management.
Additionally, machine learning and IoT platforms can analyse patterns across the production cycle, helping manufacturers identify potential bottlenecks and inefficiencies before they impact the production process.
While much of this technology is controversial as it makes human intervention progressively obsolete, it has tried-and-tested accuracy and precision rates, proving beneficial for the manufacturing sector and ensuring long-term sustainability.
Supply Chain and Inventory Management
Integrating IoT systems into supply chain management has proven transformative for manufacturing companies, improving visibility, operational efficiency, and responsiveness. Manufacturers can collect and analyse real-time metrics across the entire supply chain by using IoT applications to interconnect various devices, sensors, and systems.
GPS trackers and RFID tags provide continuous visibility of goods in transit, allowing manufacturers to monitor both the location and condition of incoming shipments. This helps them plan ahead by anticipating disruptions and managing logistics more efficiently.
IoT-connected smart sensors track real-time inventory management levels in warehouses and integrate seamlessly with pre-existing workflows. For example, if an IoT system detects a shortage of specific products or materials, it can trigger an automatic reorder, preventing bottlenecks in production. This has proven instrumental in cost-saving and stockout prevention efforts across the industry.
Furthermore, data analytics is crucial to customer satisfaction by ensuring that products are available when needed, reducing delays, and enhancing supply chain efficiency.
Energy Management and Equipment Failure Prevention
IoT applications help manufacturers monitor energy efficiency across various manufacturing operations, enabling them to identify inefficiencies and optimise energy consumption. By analysing this data, manufacturers can implement data-driven efficiency measures, leading to reduced costs and a smaller environmental footprint.
A typical example of IIoT in energy efforts is through sensors. These collect data on energy usage across various equipment and production processes, providing detailed insights into consumption patterns and highlighting inefficiencies.
Another application of IoT technology in energy management is predictive maintenance. Manufacturers can prevent excessive energy waste by predicting potential failures and scheduling maintenance proactively due to equipment failure or faulty machinery. Machine learning algorithms enhance this process by continuously improving maintenance scheduling and failure predictions.
Beyond energy efficiency benefits, predictive maintenance enhances workplace safety, minimises unplanned downtime, and improves manufacturing operations.
The Future of IoT in Manufacturing and Current Challenges
The development of manufacturing companies runs parallel with the advancement of IoT technology, machine learning, and artificial intelligence (AI). The advent of Industry 4.0 has proven that IoT-enabled systems are an integral part of modern-day manufacturing operations, driving continued innovation.
Adopting edge computing, AI-powered data analytics, digital twins, and 5G connectivity will further diversify IoT applications across industrial IoT ecosystems. As companies worldwide continue investing in digital twins and data-driven decision-making, the future of smart manufacturing looks promising. Manufacturing companies and factory workers alike can expect further strides in efficiency and automation, with sustainability at the forefront.
However, IoT-enabled adoption still faces challenges, particularly in cybersecurity, scalability, and legacy system integration. Ensuring secure data exchange and mitigating risks associated with IoT platforms will be critical to sustaining long-term growth. Despite these challenges, IoT systems are here to stay and will continue transforming manufacturing operations across industries.
The future is IoT technology, and now is the prime time for manufacturing companies to implement and scale these innovations.
How We Can Help
At Iotie, we provide IoT-enabled manufacturing solutions compatible with networks across over 150 countries—all from a single SIM card. We deliver the reliable connectivity necessary for all IoT applications in manufacturing operations.
By harnessing the power of IIoT, IoT-enabled sensors, trackers, and artificial intelligence-driven data analytics, we enable manufacturers to streamline processes, improve product quality, enhance operational efficiency, and reduce equipment failure.
Contact us today to see how we can help future-proof your industrial IoT ecosystem using IoT technology.